High-temperature heat pumps support decarbonisation
As part of the upgrades to its energy efficiency and treatment of water, the Erlangen sewage treatment plant required a cutting-edge system design for its sludge drying process. Supplied by Smardt OPK Chillers GmbH, four high-temperature heat pumps with BITZER CSH compact screw compressors at their core form the central part of the system. The renewable sludge drying process will reduce CO₂ by up to 18000 t per year at the sewage treatment plant.
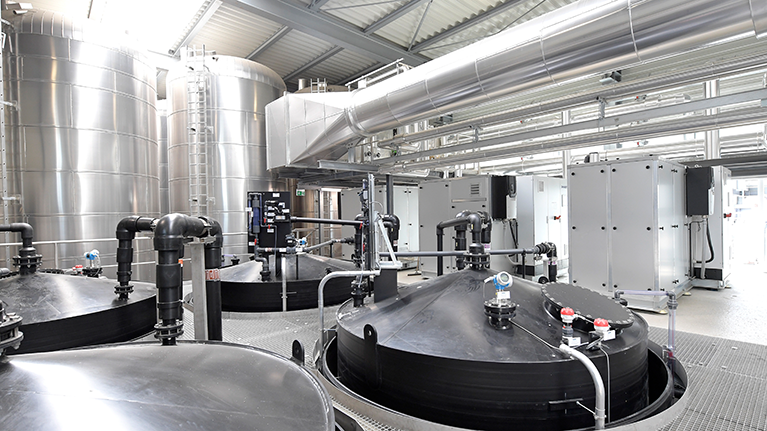
The new sludge treatment system in the Erlangen sewage treatment plant shows how the use of heat pumps to heat and cool water at the same time makes it possible to realise highly efficient, environmentally friendly thermal energy management systems. The high-temperature heat pumps (HP 1 to HP 4) at the sewage treatment plant are designed to operate as liquid chillers and recover all the condenser heat. They are controlled via the cold water outlet temperature. The cooled water is required for essential steps of the sludge treatment process. Heat recovery also provides the heating energy necessary for the industrial process of drying sewage sludge (belt drying) at high temperatures.
Reducing carbon emissions with dried sludge
The new belt-drying sludge treatment system at the Erlangen sewage treatment plant began operating in July 2023. The plant’s waste water treatment process generates up to 15700 t of sludge annually. The sewage treatment plant was designed to have enough capacity for 350000 population equivalents, i.e. human inhabitants and equivalent industrial waste water. The sludge is stabilised effluent sludge with a high water content. After dehydration and drying, it can even be used as fuel. With the new belt dryer, the average quantity of sludge per year can be reduced to a dry residue of 90 per cent and the volume by around 70 per cent. This reduces not only the costs of disposal and transportation, but also the carbon emissions, as fewer trucks are required for transport.
Demand for heat pump expertise in large capacity range
When it came to planning the sludge treatment system as a whole – under the responsibility of the Nuremberg-based engineering firm Ingenieurbüro Miller – it was crucial to ensure energy-neutral operation at the sewage treatment plant. Treated waste water is available at all times, and is therefore the optimal heat source for using high-temperature heat pumps to supply thermal energy. It was ultimately the high-temperature heat pumps that convinced the operators and engineering firm Ingenieurbüro Miller of the expertise provided by Smardt OPK (manufacturer) and Grötsch Energietechnik (overall plant engineering heating).
The heat pumps in the sewage treatment plant are used to maximise energy efficiency, as well as to heat and cool water. ‘One special feature is that the heat pumps are able to achieve the necessary hot water outlet temperature of 90°C in only a two-stage compression process (cascade) at a cold water outlet temperature of 20°C’, says Uwe Lotzmann, who is in charge of project engineering and sales at Smardt OPK. In combination with the sewage treatment plant’s existing combined heat and power and a photovoltaic system, the operation of the belt dryer is expanded into an integrated overall system.
To conceptualise and design the heat pumps, Smardt OPK worked closely with its long-term partner BITZER, the specialist in refrigeration, air conditioning and heat pump technology. BITZER has a wide range of products for industrial heat pumps with an effective temperature range of up to 95°C – from compressors and heat exchangers to electronic components. ‘Large heat pumps are the cornerstone of a green, future-proof energy economy, which is why we at BITZER have been working on development in this field for many years’, says Dirk Schlehuber, Product Manager for Screw Compressors at BITZER.
Heat pump: heating and cooling combined efficiently
The identical heat pumps HP 1 and HP 2 in the sewage treatment plant’s new machine room are designed as thermal cascade systems, each with two coupled refrigerant circuits. In each of the two heat pumps, a CSH7593-90Y-40P compact screw compressor and a CSH8583-125Y-40P compact screw compressor from BITZER deliver the necessary heating and cooling capacity in the low and high temperature stages (LT and HT stages) respectively. Their compact dimensions, thanks to the built-in oil separator, make CSH compressors ideal for a system design that saves space. It takes the refrigerating capacity of both heat pumps together, 470 kW in total, to cool water with a flow temperature of 20°C to operate a cooling water exhaust air scrubber for the purposes of sludge treatment.
On the condenser side of the heat pumps, water is heated to a flow temperature of 90°C and stored in eight thermally insulated storage tanks from Grötsch Energietechnik, each with a volume of 107 m3. The hot water, at a temperature of 90°C, is supplied to the belt dryer from the storage tank battery, which has a total capacity of 856 m3. The total heating capacity of the two heat pumps HP 1 and HP 2 is 760 kW. At nominal conditions, this results in an overall refrigeration and heating efficiency of 4.24 in combined stationary operation.
The single-stage heat pump HP 3 is directly adjacent to the two cascade systems in the new machine room. The CSH8583-125Y-40P semi-hermetic compact screw compressor delivers a refrigerating capacity of 117 kW and a heating capacity of 181 kW. At nominal conditions, HP 3 boasts an overall efficiency of 4.1 in combined stationary operation. It supplies cold water at 30°C for sludge hydrolysis – i.e. the breaking down of organic substances by microorganisms – while also supplying hot water at 90°C through the storage tank battery to dry the sludge with the belt dryer.
Like HP 1 and HP 2, the fourth heat pump of Smardt OPK is a cascade heat pump that, although housed in a separate building, also supplies hot water to the belt dryer via the heat accumulators. In terms of refrigeration, HP 4 generates 193 kW of refrigerating capacity for cold water at 4°C. The overall efficiency of the system is 3.7 here. The significant temperature lift from 4°C to 90°C is covered by a CSH8573-110Y-40P in the LT stage of the cascade and by a CSH8583-125Y-40P compact screw compressor in the HT stage.
Coordinated system design with precise capacity control
‘Aside from the compressors, we were able to rely on our partner BITZER when it came to selecting the other components for the four heat pumps’, says Sascha Holder, project manager at Smardt OPK. This means that the systems also feature PC shell and tube evaporators from BITZER as well as CRF shell and tube condensers. As the heat pumps in the sewage treatment plant work with treated waste water, shell and tube systems are an exceptionally good choice: their large flow cross sections make them resistant to dirt, they can be cleaned when necessary and they are robust under thermal stress. Additionally, heat exchangers inside all the refrigerating circuits ensure that the refrigerant is sufficiently superheated. This way, they ensure that safely superheated suction gas is taken in through the compressors, which improves operating reliability. At the same time, the system’s performance is increased by the high subcooling of the refrigerant.
To guarantee energy-efficient system operation, the experts at Smardt OPK also opted to equip the heat pumps with BITZER VARIPACK frequency inverters. These are precisely adapted to the motor characteristics of the BITZER compact screw compressors. The result is a system operating with optimal cos-phi values, minimal power loss and precise compressor capacity adjustment based on the heating or cooling demand – in both full load and part load operation. When the three cascade heat pumps were commissioned in the sewage treatment plant, the frequency inverters even simplified load management during start-up operation: the frequency inverters start the compressors with a low starting current (soft-start feature) so as to avoid higher starting currents like with the star-delta start.
‘We and our customer Smardt OPK opted for the SE-i1 compressor protection device for this special application. It monitors all the key operating parameters of the screw compressors, such as discharge gas and oil temperature and PTC resistance in the motor, and provides access to the BITZER Digital Network (BDN)’, explains Benjamin Vornweg, Technical Consultant at BITZER. With the myBITZER online platform, Smardt OPK can observe, evaluate and optimise the operating data of the compressors at any time.
A sewage treatment plant that serves as a role model
With its cutting-edge system concept and the potential to save 18000 t of CO₂ per year with the sludge drying process, the Erlangen sewage treatment plant is pioneering the decarbonisation of sewage management. Using high-temperature heat pumps to heat and cool water simultaneously makes it possible to achieve excellent annual performance figures and realise efficient, environmentally friendly industrial systems. ‘We are delighted that we were able to win over the engineering firm and operator for our products and services with the help of BITZER and contractor Grötsch Energietechnik,’ says Uwe Lotzmann.
Further information on the companies involved
- Visit Smardt OPK Chillers Website
- Visit Grötsch Energietechnik Website
- Visit Ingenieurbüro Miller Website