Utilising existing energy potential sustainably
Since November 2023, a large heat pump at SFS Group Schweiz AG has been utilising waste heat from production processes to heat buildings on the company premises in Heerbrugg. This is an important step towards decarbonisation. By providing heating water temperatures of up to +75°C, the heat pump replaces a fossil-fuelled boiler. The centrepiece of the heat pump is a powerful compact screw compressor from BITZER’s CSV series. Scheco AG was responsible for the overall planning and implementation of the customised system concept, including the measurement, control and regulation technology.
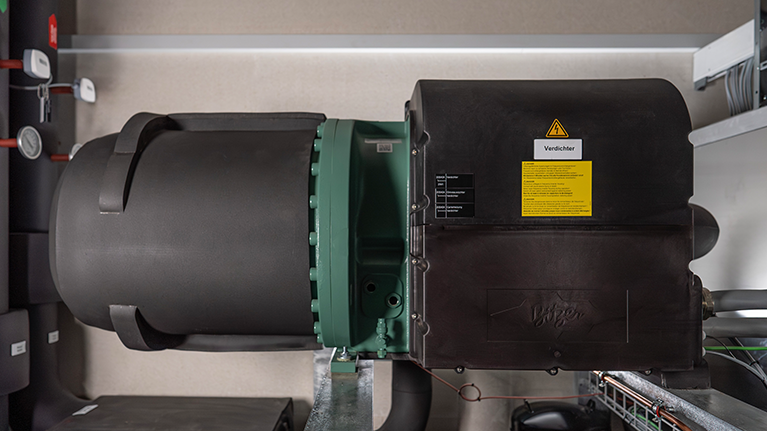
BITZER IN ACTION #1 with Scheco AG
The SFS Group is a global leader in application-critical, high-precision components and assemblies, mechanical mounting systems, high-quality tools and management solutions. The company uses groundwater from its own well to cool production processes at its location in Heerbrugg. The cooling water is then captured in a collecting basin with a capacity of 80 m3 before being released into the nearby river. In order not to leave the energy of industrial waste heat unutilised and to increase overall energy efficiency, a water-to-water heat pump was to be implemented and integrated into the existing heating system for the building heating. The SFS Group is increasing the percentage of renewable energies at the company one step at a time in an effort to reduce its CO₂ emissions. ‘For the project, we needed a partner with the expertise necessary to plan and design the entire heat pump system,’ says Claudio Winter, Head of Infrastructure at the SFS Group.
Tailored system concept required
A customised system concept was essential for the technical and economic implementation of the heat pump, taking into account the specific customer requirements. ‘It is important to us to utilise synergies in the best possible way,’ says Marc Grünig, Managing Director of Scheco. The core of the system is the BITZER CSV compact screw compressor that ensures high efficiency in a compact size.
According to the customer, the new heat pump needed to be integrated into the existing heating system, with clearly defined prioritisation of energy sources. The buildings on the premises had been heated using four gas/oil boilers as well as the heat recovered from the waste heat produced through air compression. In a first step, the heat generated from the compressed air is now fully utilised for heating the building before the heat pump is used on demand. Heat will only be generated with fossil fuels when demand increases. This form of prioritisation ensures the ideal use of existing energy sources on the company grounds.
Eco-friendly alternative to heat generation with fossil fuels
The collecting basin for the cooling water from production, which serves as a source for the heat pump, is located in the basement of a different building than the heating centre in which the heat pump is installed. A decisive factor in the design of the heat pump was the in-depth analysis of the source, taking into account the varying volume flows on the primary side due to the different production machines that are currently in use and require cooling water. In summer 2023, the collecting basin was equipped with a laminated metal sheet, a circulation pump and temperature sensors for integration into the heat source circuit. It was also hydraulically integrated into the intermediate circuit via two plate heat exchangers.
An existing pipeline, which had been installed under the roadway during construction of the building that houses the water basin in preparation for future projects, was used to connect the basin to the heating system. This pipeline delivers the water of the intermediate circuit to the flat plate evaporator of the heat pump, which absorbs heat from the water and transfers it to the refrigerant. This project called for a variable source as well as different operation modes for the heat sink, which played a key role when it came to selecting system components for the heat pump. The heat pump therefore needs to be able to reliably supply the necessary heating capacity even in highly fluctuating operating conditions. The core of the system is the compressor. ‘Modulation has clearly revealed that the design of the application range and compressor regulation needs to be variable,’ explains Marc Grünig. A compact screw compressor from the BITZER CSV series, which is characterised by a wide power modulation range, was chosen. ‘We opted for BITZER because of the quality of its products and because of the successful partnership we have had for years,’ says Marc Grünig. The suction gas cooled built-in motor and the integrated, refrigerant-cooled frequency inverter are optimally coordinated and combine efficiency with a compact design. The compressor also has a high-speed screw profile, which was developed with the aid of state-of-the-art flow simulations and enables speeds of up to 6400 1/min. The power electronics of the integrated frequency inverter are cooled with refrigerant on a continuous basis, ensuring safe and reliable system operation. The CSV series also boasts automatic Vi adjustment in line with the most common system conditions like the pressure ratios specific to the current operating conditions, thus enabling compressor operation in the optimal and thus efficient range.
On the safe side
Considering the location of installation and the stringent safety requirements, a decision was made to use a low-GWP A2L refrigerant for the application. To fulfil requirements, Scheco developed a customer-specific safety concept for the heat pump which keeps all the system parts containing refrigerant in a separate space inside the machinery room. This space is equipped with protection devices such as a gas warning system and ventilation. The system is controlled using the safety switch cabinet positioned outside of the space, which activates ventilation and separates all the heat pump components from the voltage supply if a refrigerant leak is detected. These structural features required extremely compact system dimensions, which the CSV compressor enables thanks to its integrated frequency inverter and the suction gas cooled motor. The compressor is also connected to the BITZER Digital Network (BDN) via a gateway in the switch cabinet, which provides access to its detailed operating data at all times for evaluations and optimisations. Scheco can access these data at any time via the myBITZER online platform.
Beneficial for the environment and more
The SFS Group’s new heat pump delivers heating capacity of up to 930 kW and can provide hot water temperatures of up to +75 °C for heating buildings on the premises. An example of how industrial waste heat can be converted into usable heating energy. This capacity has allowed the SFS Group to fully replace a fossil fuel oil/gas combination boiler with the heat pump. ‘This project demonstrates that there’s a great deal of potential energy available at industrial companies, which can be used to drive forward decarbonisation,’ says Marc Grünig. The climate-friendly system boasts an efficient COP and has therefore proven to be an economically attractive alternative. The SFS Group was also able to take advantage of energy funding provided by the Swiss government for its investment in the system. The company is very satisfied overall with how the project has progressed and hopes that more and more similar concepts for using waste heat in industrial environments will be established.
More information on Scheco AG: Visit Sheco website
More information on SFS Group Schweiz AG: Visit SFS Group Website
Contact us for more information